A Comprehensive Guide to the Process and Advantages of Plastic Extrusion
In the huge world of manufacturing, plastic extrusion becomes a extremely effective and essential procedure. Transmuting raw plastic into constant profiles, it provides to a huge selection of markets with its exceptional versatility. This overview intends to elucidate the intricate actions entailed in this approach, the kinds of plastic suitable for extrusion, and the game-changing advantages it brings to the sector. The taking place discussion assures to unfold the real-world influences of this transformative procedure.
Understanding the Fundamentals of Plastic Extrusion
While it might appear complex at initial glance, the process of plastic extrusion is fundamentally easy. The procedure starts with the feeding of plastic product, in the type of powders, pellets, or granules, right into a warmed barrel. The shaped plastic is then cooled, strengthened, and cut into wanted sizes, finishing the procedure.
The Technical Refine of Plastic Extrusion Explained

Sorts Of Plastic Suitable for Extrusion
The choice of the ideal kind of plastic is a crucial facet of the extrusion process. Numerous plastics supply special residential properties, making them more suited to specific applications. Polyethylene, for instance, is frequently used because of its low cost and simple formability. It supplies outstanding resistance to chemicals and dampness, making it perfect for items like tubes and containers. In a similar way, polypropylene is one more popular option because of its high melting point and resistance to fatigue. For more durable applications, polystyrene and PVC (polyvinyl chloride) are typically selected for their toughness and sturdiness. These are usual choices, the option eventually depends on the specific needs of the product being produced. So, understanding these plastic kinds can significantly boost the extrusion procedure.
Contrasting Plastic Extrusion to Various Other Plastic Forming Methods
Comprehending the kinds of plastic ideal for extrusion paves the method for a wider discussion on how plastic extrusion stacks up against various other plastic developing approaches. Plastic extrusion is unmatched when it comes to developing continuous profiles, such as gaskets, pipelines, and seals. It additionally allows for a regular cross-section along the size of the item.
Secret Benefits of Plastic Extrusion in Production
In the realm of manufacturing, plastic extrusion uses lots of substantial advantages. One significant advantage is the cost-effectiveness of the procedure, that makes it a financially enticing manufacturing technique. Additionally, this strategy gives premium item versatility and improved production rate, therefore boosting general manufacturing performance.
Cost-efficient Manufacturing Approach
Plastic extrusion leaps to the forefront as an economical production method in manufacturing. Additionally, plastic extrusion requires much less power than conventional manufacturing methods, contributing to lower operational costs. Overall, the financial benefits make plastic extrusion a very attractive option in the manufacturing market.
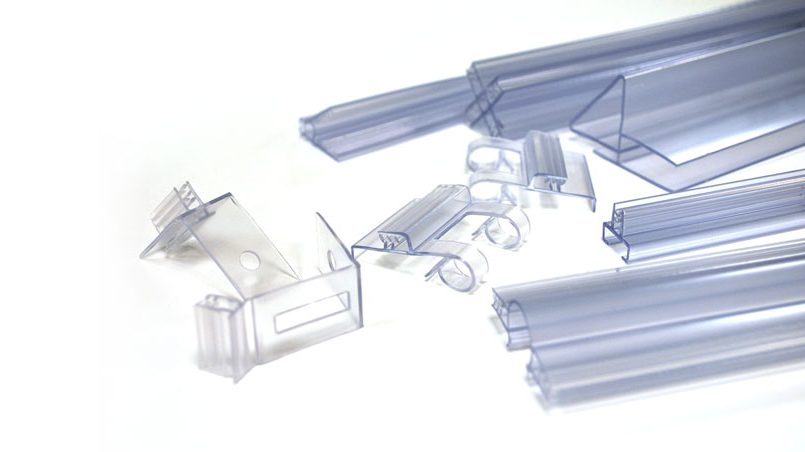
Superior Item Versatility
Past the cost-effectiveness of plastic extrusion, an additional significant benefit in making lies in its exceptional item versatility. This makes plastic extrusion a content perfect option for sectors that require tailored plastic elements, such as vehicle, building and construction, and packaging. In significance, plastic extrusion's item next page adaptability fosters advancement while enhancing operational effectiveness.
Boosted Production Speed
A considerable advantage of plastic extrusion hinges on its improved manufacturing speed. This production procedure permits high-volume manufacturing in a relatively brief time period. It can producing long, constant plastic profiles, which substantially reduces the production time. This high-speed production is specifically helpful in industries where big amounts of plastic components are required within tight deadlines. Couple of various other production procedures can match the speed of plastic extrusion. Additionally, the capacity to keep constant high-speed production without sacrificing item quality sets plastic extrusion in addition to other approaches. The boosted manufacturing rate, therefore, not only enables producers to fulfill high-demand orders however likewise adds to enhanced effectiveness and cost-effectiveness. This helpful function of plastic extrusion has made it a preferred choice in various sectors.
Real-world Applications and Effects of Plastic Extrusion
In the realm of production, the method of plastic extrusion holds extensive relevance. This process is extensively used in the manufacturing of a variety of products, such as plastic tubes, window frameworks, and weather condition removing. As a result, it significantly affects markets like construction, product packaging, and automotive industries. Additionally, its impact encompasses daily things, from plastic navigate to this website bags to toothbrushes and non reusable flatware. The financial advantage of plastic extrusion, primarily its affordable and high-volume outcome, has actually changed manufacturing. Nonetheless, the environmental effect of plastic waste continues to be a worry. As a result, the market is persistently aiming for developments in recyclable and naturally degradable products, showing a future where the advantages of plastic extrusion can be kept without jeopardizing environmental sustainability.
Verdict
To conclude, plastic extrusion is a extremely effective and reliable method of transforming raw materials into varied products. It provides various advantages over other plastic forming approaches, consisting of cost-effectiveness, high output, very little waste, and design adaptability. Its impact is profoundly felt in different markets such as building and construction, automotive, and durable goods, making it a critical process in today's manufacturing landscape.
Digging much deeper right into the technical process of plastic extrusion, it begins with the choice of the appropriate plastic material. Once cooled, the plastic is cut into the needed lengths or wound onto reels if the product is a plastic film or sheet - plastic extrusion. Comparing Plastic Extrusion to Other Plastic Forming Approaches
Recognizing the kinds of plastic ideal for extrusion paves the way for a broader conversation on how plastic extrusion stacks up versus other plastic forming approaches. Couple of various other manufacturing processes can match the speed of plastic extrusion.
Comments on “Plastic extrusion for large-scale custom plastic parts”